English page navigation
The Challenge of Realizing “KATACHI”
―TAKAHASHI SEIKI value your commitment to “KATACHI” means your “product images” and “realized products”.
SCROLL
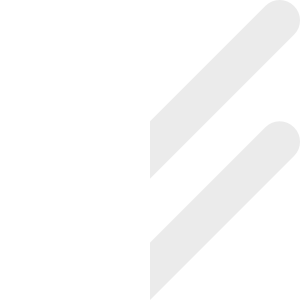
Mold Making
Molding and Mass
Production
3D Digitizing
Molding Machine
TAKAHASHI SEIKI – the manufacturer of special molds for plastic molding
We have been working together with our customers to solve their problems, such as “Can you make this?” “We’re on the verge of giving up because we’ve been turned down elsewhere.” Please contact us to discuss any difficulties you may have.
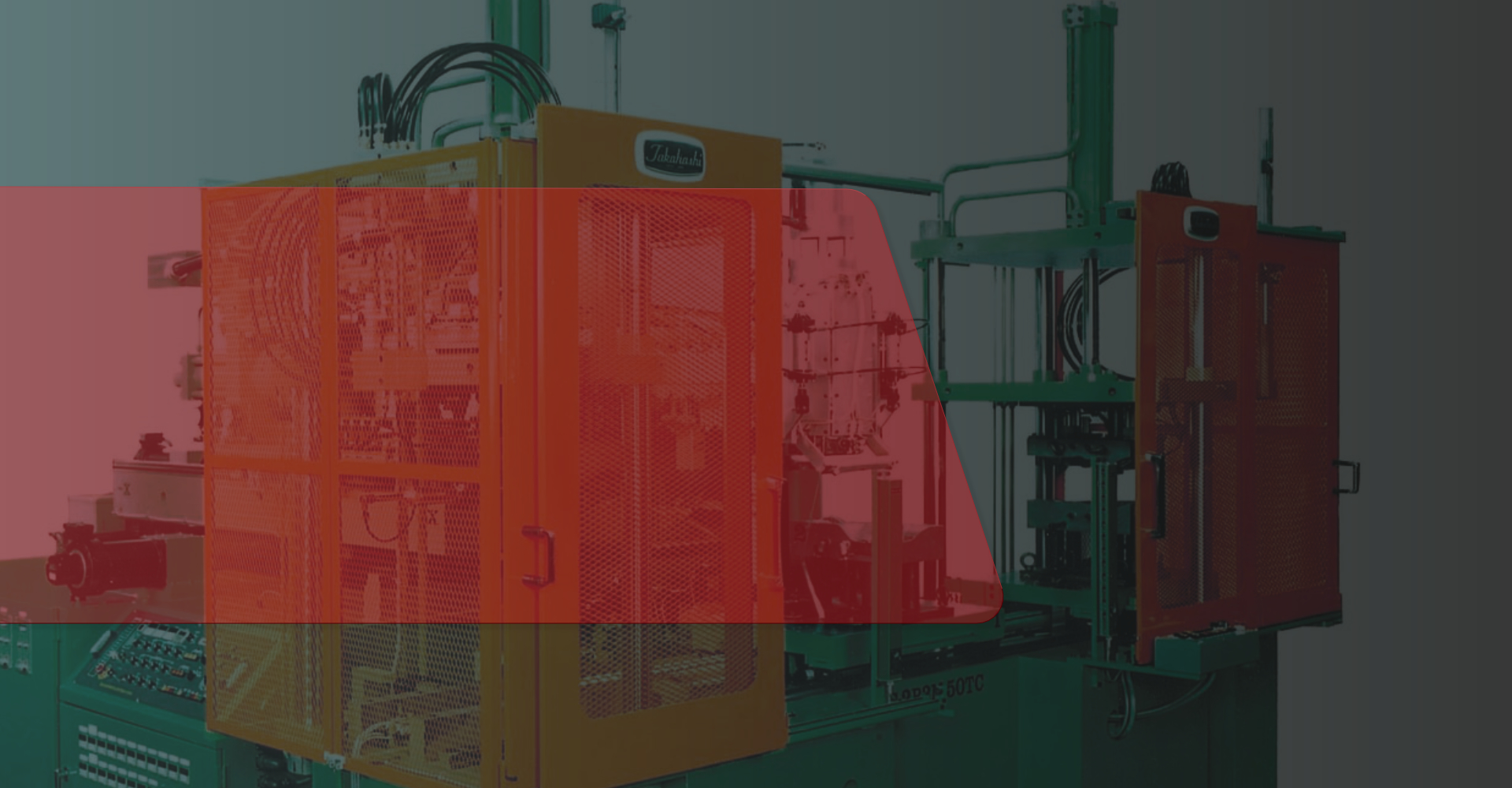
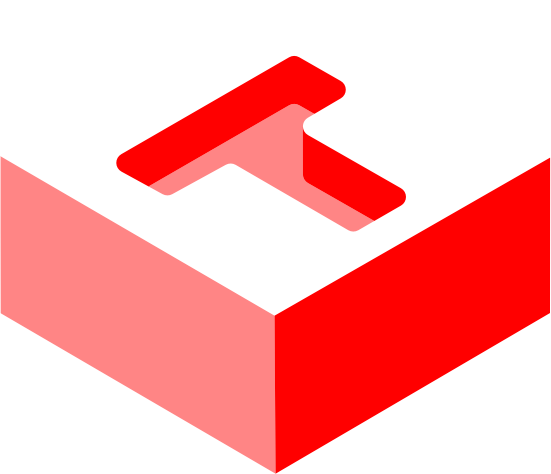
Our technolory
What is TAKAHASHI SEIKI?
The company specializes in special mold fabrication, mainly for multi-color, multi-material molding.
Since establishing two-color molding technology in the 1950s, we have been working with customers in various industries on everything from research and development to the manufacture of molding machines and molds, and the mass production of molded products, with a focus on the molding of multi-materials.
In particular, we have earned an excellent reputation for 2 color molding and glass insert molding.
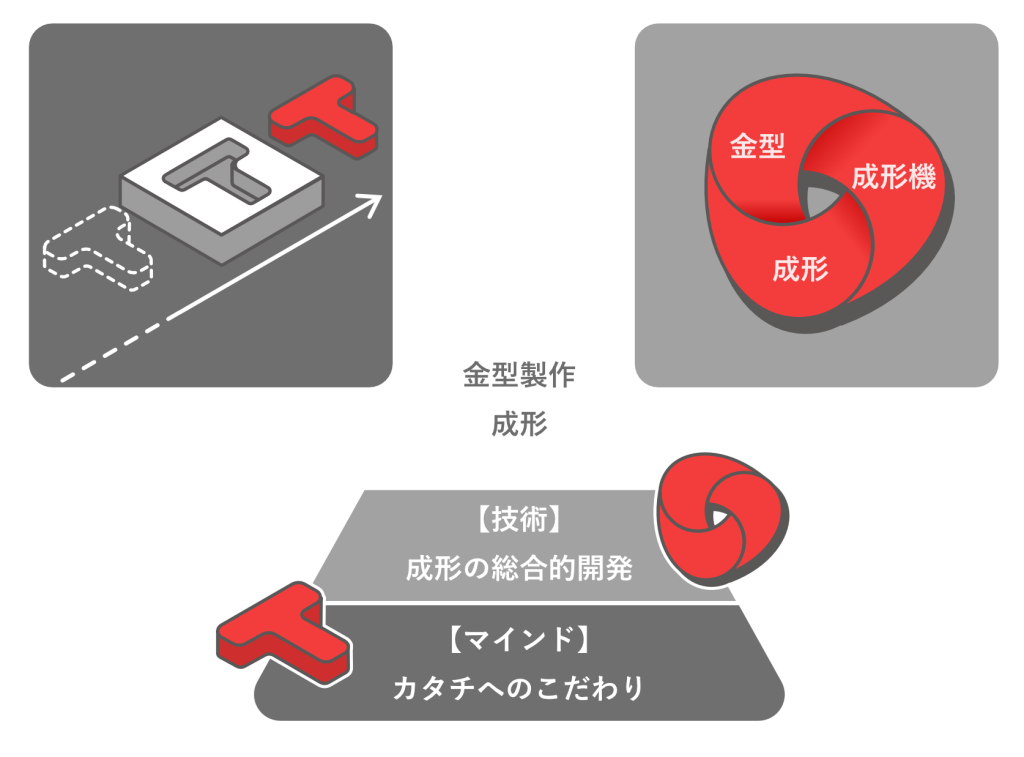
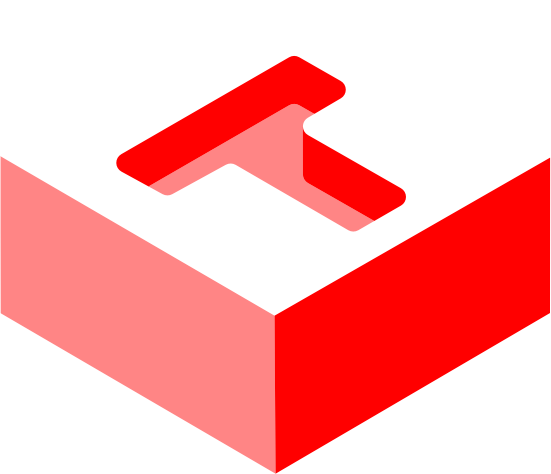
PICK UP technology
TAKAHASHI SEIKI’s Mold Technology
We have a high reputation for quality. Especially, we focus on the following three technologies.
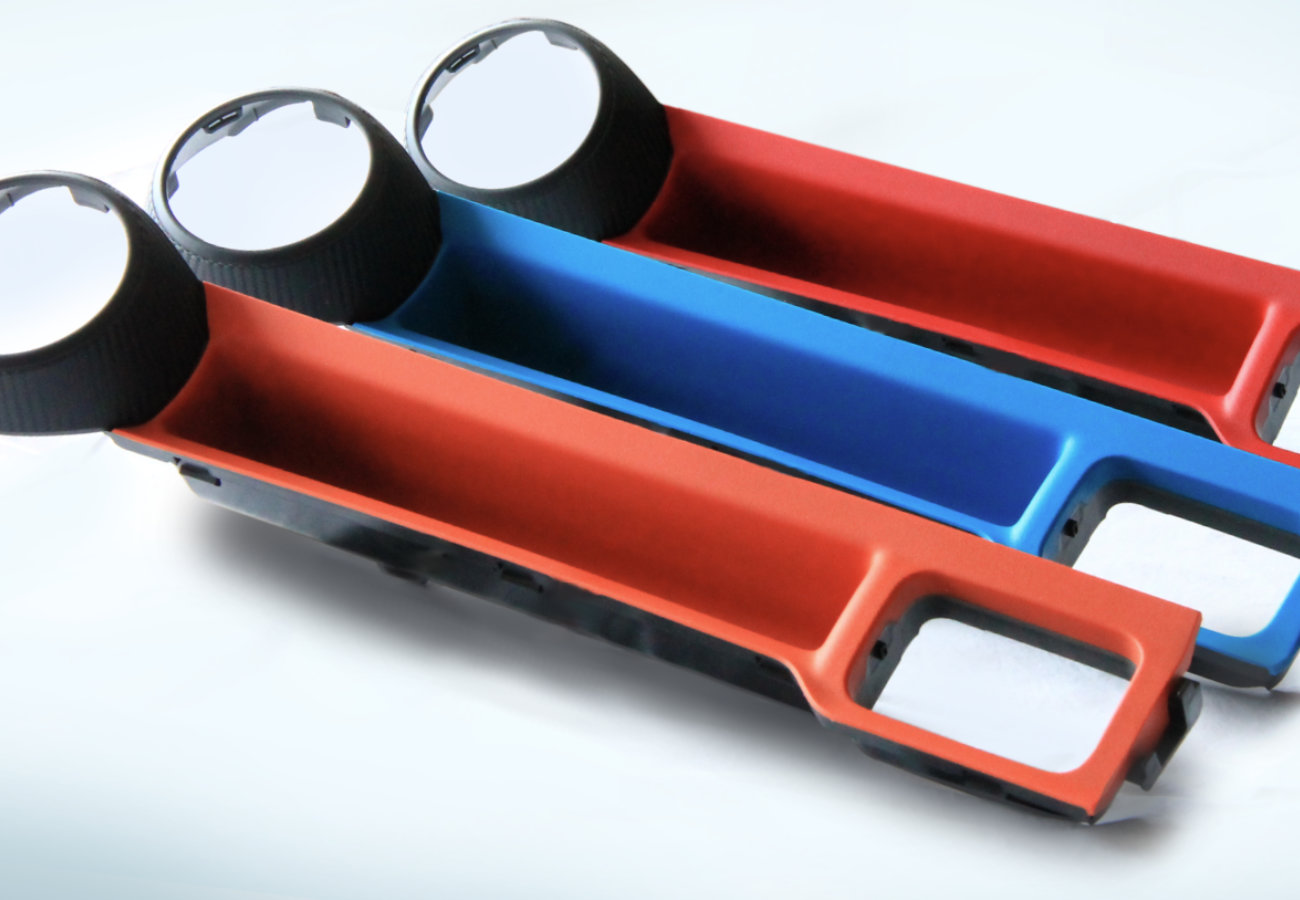
Multi-color, Multi-material Molding (2 Color Molding)
This is the first technology TAKAHASHI SEIKI has realized in Japan to mold multiple plastics into a one-piece molded product.
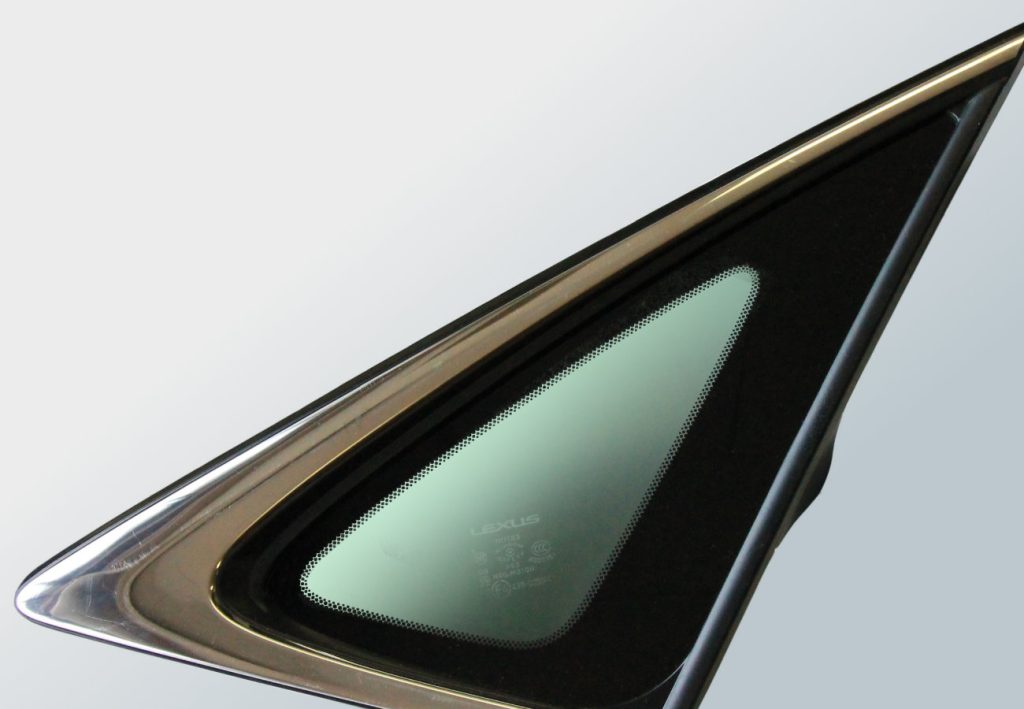
Insert Molding (Glass Encapsulation Molding)
This is a technology that inserts parts made of different materials into a mold before molding to form them into a one-piece molded product.
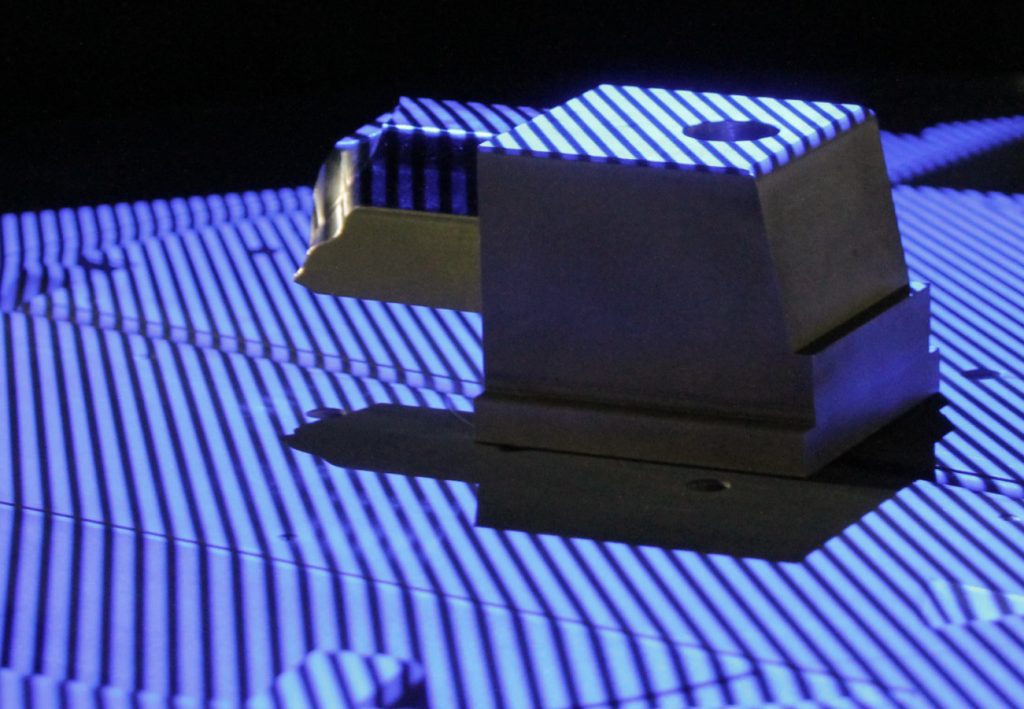
3D Digitizing Technology (Reverse Engineering)
Using a 3D scanner, drawings and molds can be recreated from existing molds or molded products.
English page navigation
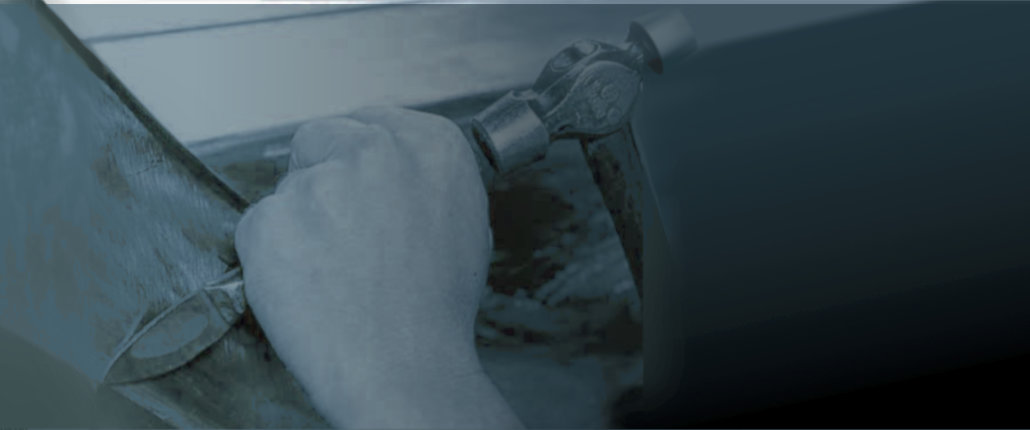
TAKAHASHI SEIKI’s Technology
Pursuing “KATACHI”
“KATACHI” is a combination of a “mold” to realize an image and a realized “product”.
TAKAHASHI SEIKI makes new “KATACHI” in the world through our mold technology.kes new “product images” in the world through our mold technology.
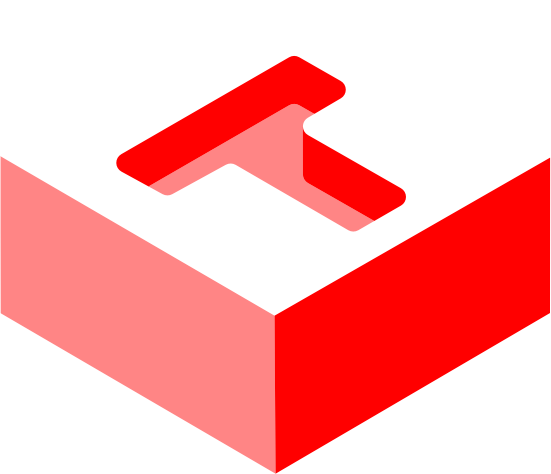
Reason for high quality
Why can we create new mold technology?
TAKAHASHI SEIKI has realized many products that were said to be difficult to realize with plastic molds.
Here are three of the secrets.
Creation of product images brings forth a new world of possibilities.ーーー
Accumulated expertise
With our development capabilities cultivated through numerous special molding achievements, we offer world-class proposals from a technological perspective.
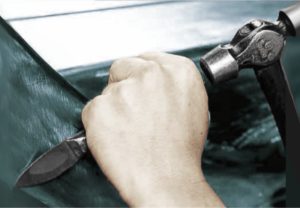
The root of our pursuit of product image lies in our pioneering spirit.
Pioneer of 2 Color Molding
The 2 color molding technology was patented based on a unique idea, and the spirit of this technology has been continued to the present day.
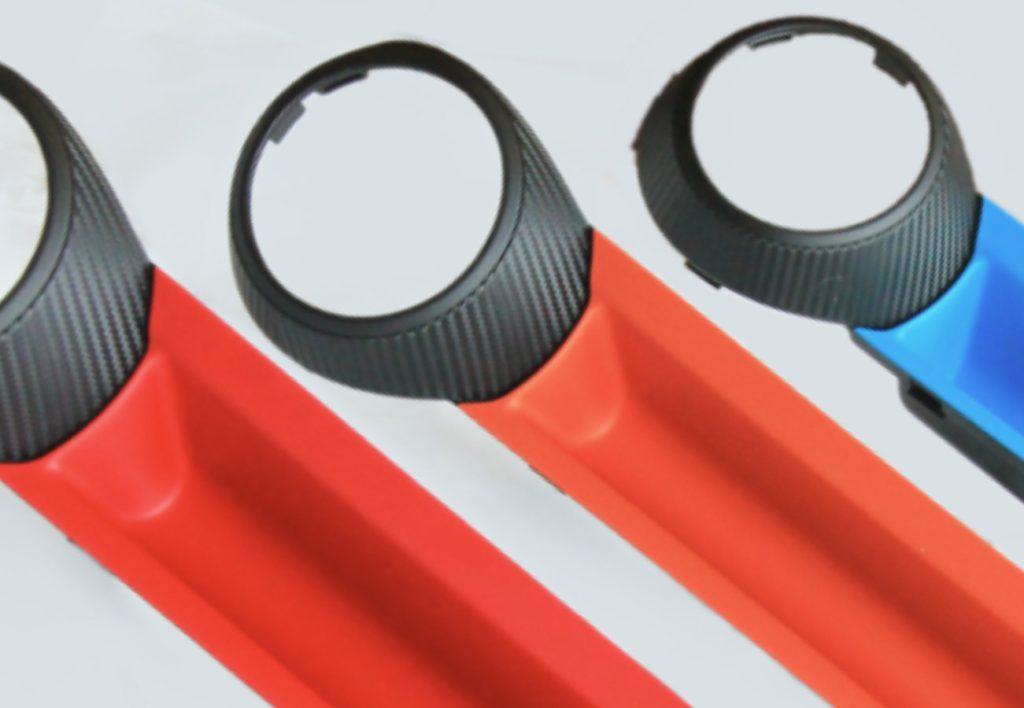
Realization of product image more as you wish
Introduction of the latest technology
We actively engage in extremely difficult challenges through our mold manufacturing process, which combines traditional craftsmanship with state-of-the-art technology.
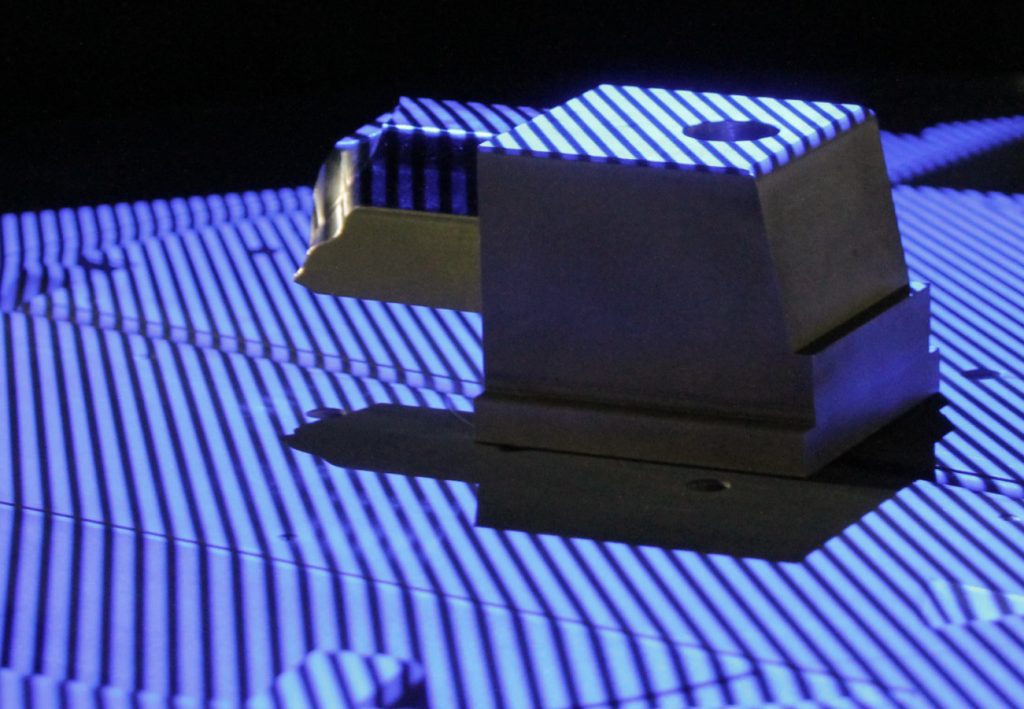
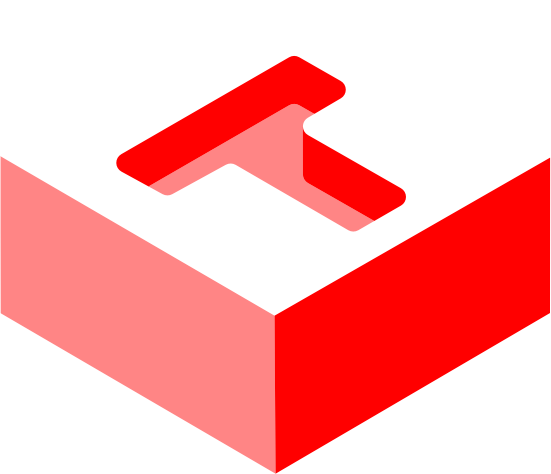
Technology policy
Commitment to the product image (action policy/values)
The “product image” that TAKAHASHI SEIKI value is the “product” embodied by using a “mold” to realize the idea.
We consider a “MOID” as a system of materialization.
Based on our research and development of molding machines, molds, and molding, we would like to explore the optimal solution for materialization together with you.
We consider a “PRODUCT” is a “mimesis = reproduction of the essence”.
As a development engineer, we understand the inevitability of such a form and make the most of our know-how to realize it.
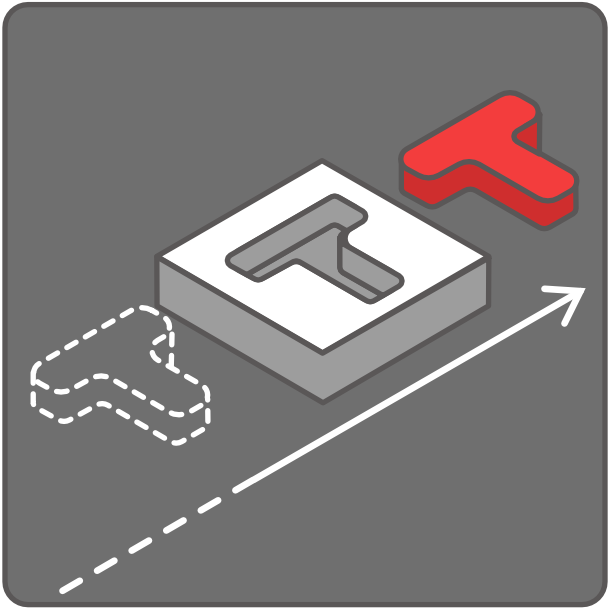
Development expertise in all plastic molding processes
TAKAHASHI SEIKI has put a great deal of effort into the development of “MOLDs,” “MOLDING MACHINEs,” and “MOLDING” respectively. These know-how are mutually reinforced and utilized as comprehensive knowledge in our current business.
MOLDs:
Skilled craftsmen who have inherited traditional craftsmanship rely on their sense of touch and intuition, while using cutting-edge technology as a tool true to their will to produce high-quality molds.
MOLDING:
A mold is only a tool, and its purpose is to mold the required product.
We also mold products that require advanced molding technology by utilizing the knowledge we have accumulated through years of working experience.
3D Digitizing Technology:
We can reproduce 3D data for molds and products for which there are no drawings or data.
MOLDING MACHINEs:
Our advanced mold making technology is based on the development of molding machines as the world’s top level.
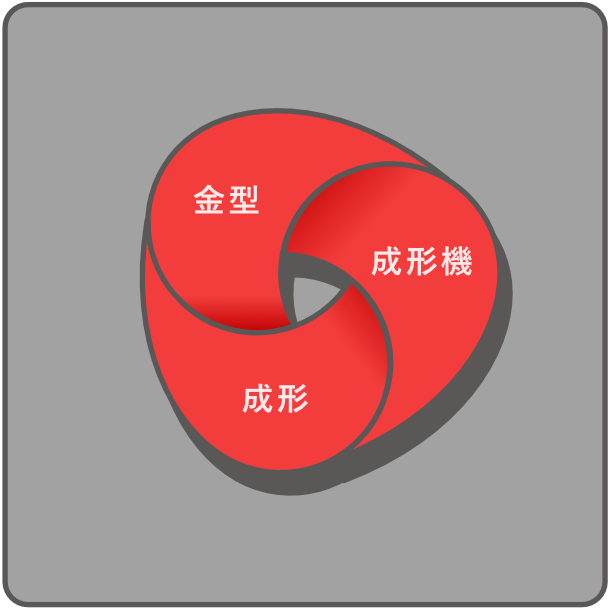
English page navigation
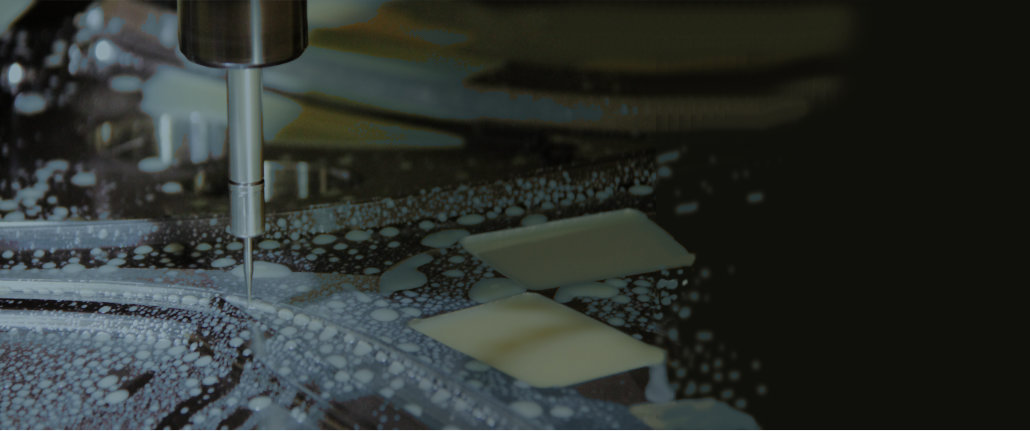
Mold
Making an image into “KATACHI”
The mold is the process of transforming a concept image into a real “KATACHI”.
Superior mold technology supports unlimited creativity, and its details are extraordinary.
We have succeeded the traditional craftsmanship and realized the mold manufacturing process with highly advanced technology.
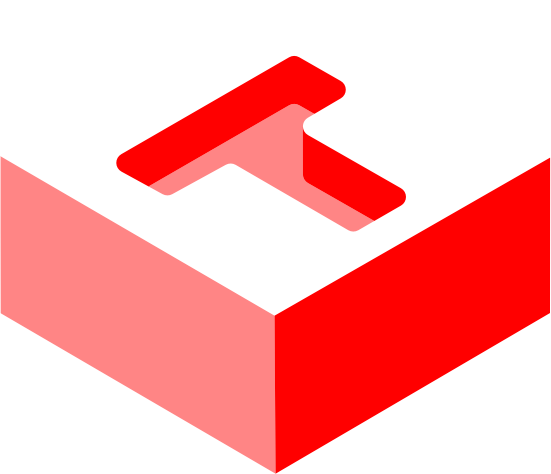
MOLD FOR PLASTIC
What is a mold for plastic molding?
Molds are an essential tool in modern mass production and the basis of production technology.
A superior mold results in a more efficient molding process and improved quality of the molded product.
TAKAHASHI SEIKI’s mold making technology is capable of handling those that require structures that are difficult to produce.
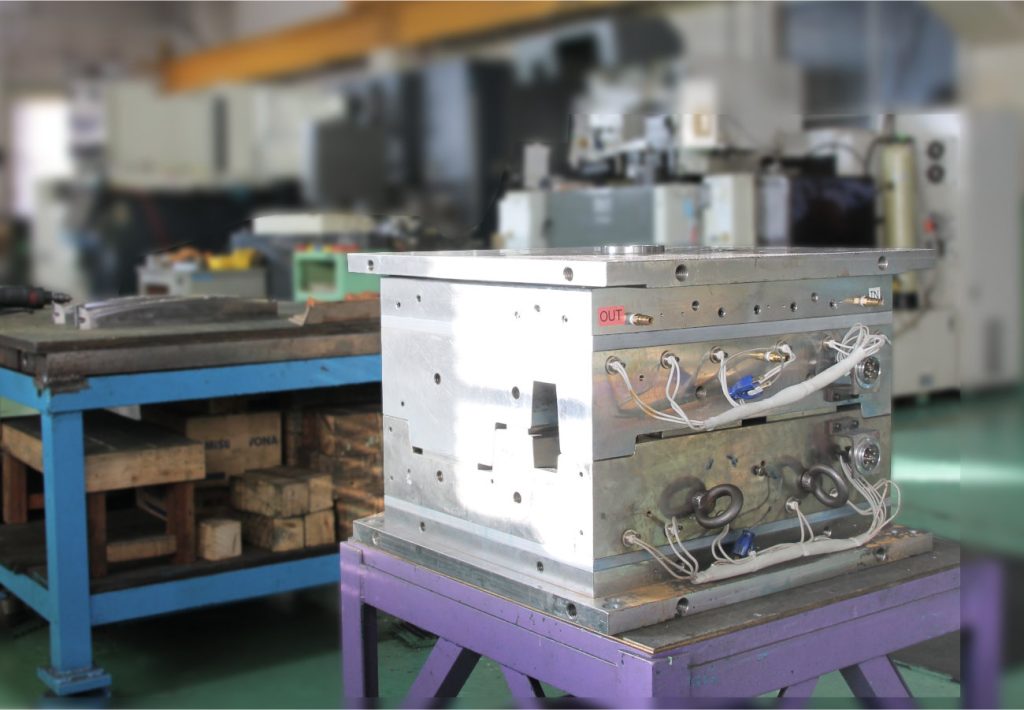
TAKAHASHI SEIKI’s specialty molds for
In particular, our multi-color, multi-material molding (two-color molding) and insert/glass encapsulation molding have been recognized as one of the most advanced technologies in Japan.
Of course, we also have enough experience in insert molding other than glass insert and general injection molding molds (for molding machines with clamping forces of 850 to 1300 tons are our strongest point).
Mold Production Experience
- Molds for multi-color and multi-material molding (2 to 4 color molding has been performed)
- Various insert molds, including for glass encapsulation molding
- All general plastic injection molds
- Molds for gas injection
- Molds for various decorative molding
- Molds for blow molding
- Molds for rubber molding etc…
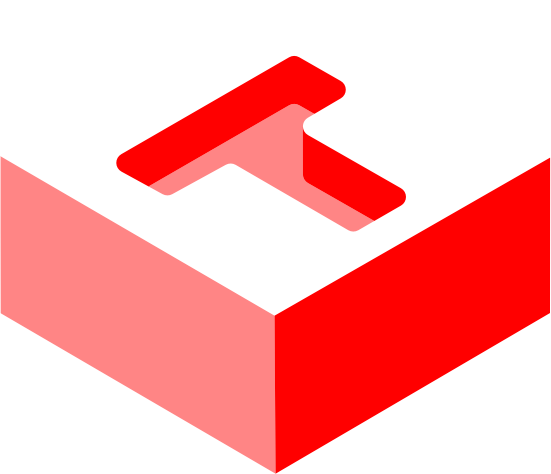
MULTICOLOR-MULTIPLE MOLDING
What is multi-color, multi-material molding (2 color molding)?
Multi-color, multi-material molding is a technology for molding products in which two or more types of resins are united. Using a specialized molding machine, resins of different colors and/or materials are injected into the mold in sequence. The resins are united inside the mold and ejected as a molded product.
2 color molding was originally started by one-piece molding of resins of the same material in different colors, and TAKAHASHI SEIKI named it “2 color molding” because of its appearance.
As the process evolved from there to 3 and 4 color molding, we pursued the functional aspect of molding with different materials, regardless of the material color.
The process requires special molding machines and molds, and the products are molded as one piece in the mold.
Features of 2 color molding
Productivity improvement
Since two colors are molded at once, later processes (assembly, painting, etc.) can be reduced, thus shortening the total lead time.
Variations and defects in later processes are also eliminated, resulting in total cost reductions.
Highly flexible design
We can produce shapes that cannot be assembled in the post-process, such as a beautiful appearance with no seams or gaps.
Improved durability by melting and bonding with each other
Depending on the choice of the two materials, the strength of the molten face by one-piece molding is stronger than that by gluing them together by melting them into each other.
Sample representative of 2 color molding
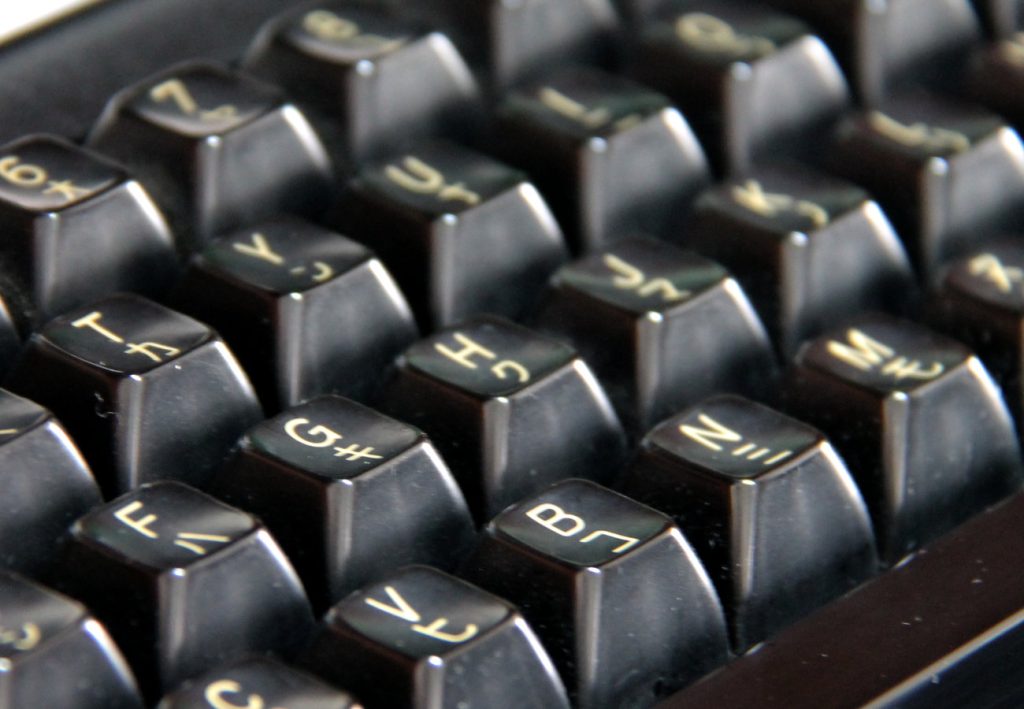
2 color molding with same material
It was first developed to prevent the letters on the key tops of typewriters (keyboards) from disappearing. This technology is also used for automobile tail lenses, which are divided into red, white, and orange.
Since the two materials are completely fused together, there is no cracking at the color border.
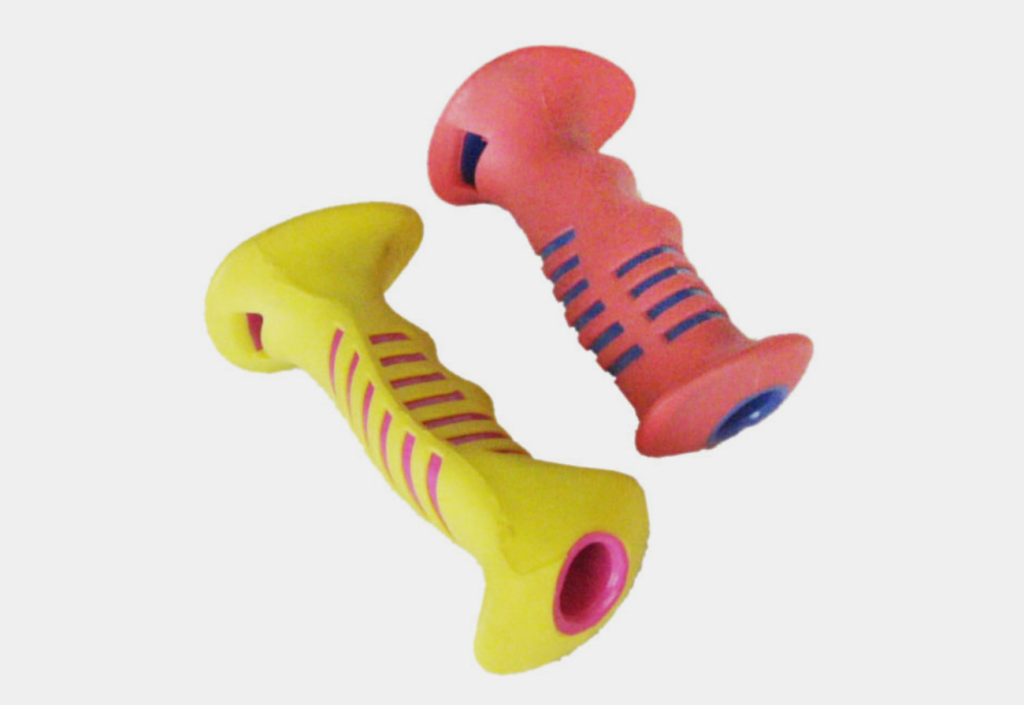
2 color molding with different materials
Hard and soft materials can be used to create different feel and grip with designs that take advantage of the materials.
For complex shaped gaskets, there are no gaps at all and the assembly process can be eliminated, which also eliminates work errors.
Materials that fuse with each other will not peel off. On the other hand, combinations that do not fuse with each other can be used for in-mold assembly of moving parts.
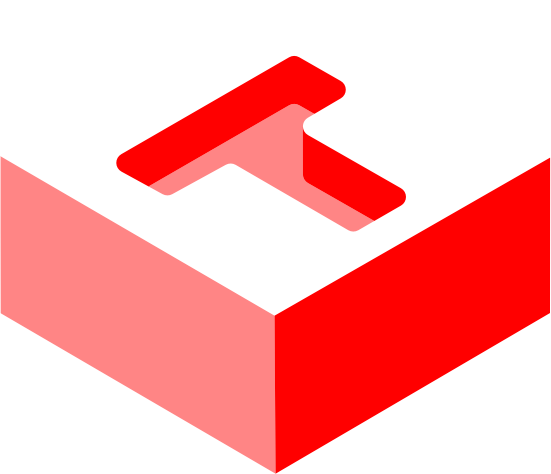
INSERT MOLDING
What is insert/glass encapsulation molding?
Insert molding is a technology in which a product of a different material is inserted into a mold and molded as one piece with resin.
It can eliminate quality variations due to assembly work after molding, and it is also possible to prevent the product from detaching from the molded part.
Glass Encapsulation is an insert molding technology that integrally molds glass and resin.
Our extensive know-how accumulated through years of joint development with glass manufacturers enables stable mass production of high quality products with minimal glass breakage.
This technology is still evolving, and we are proud to say that the quality of the finished products is among the best in the world.
Sample representative of insert molding
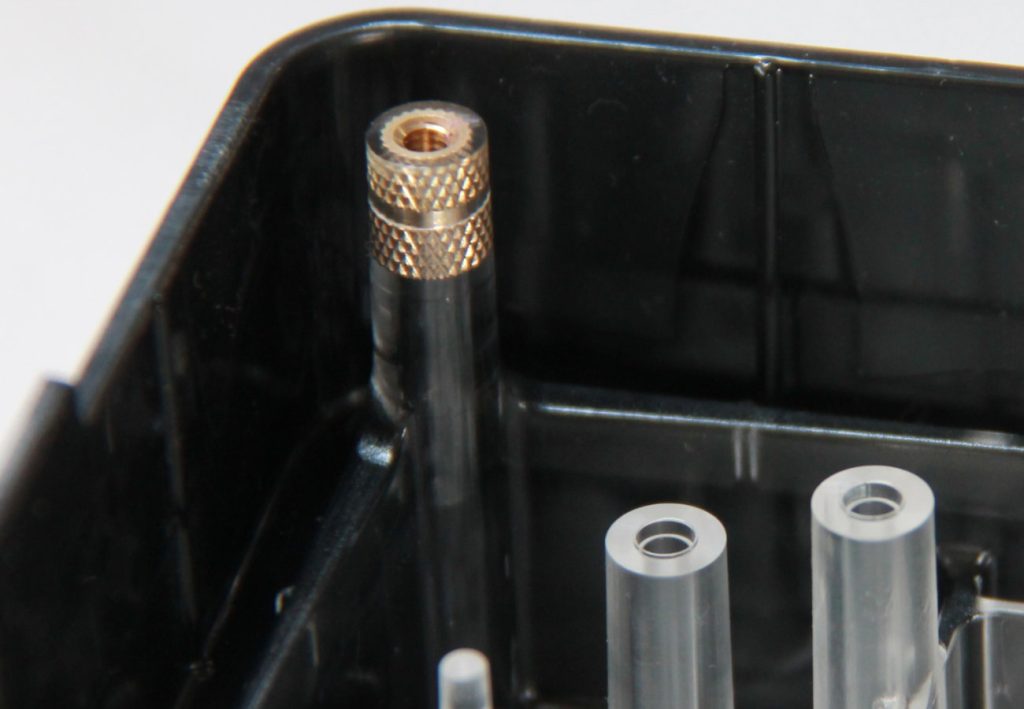
Inserts for fastening parts
Can be embedded to keep bolts, nuts, clips, etc. from coming off.
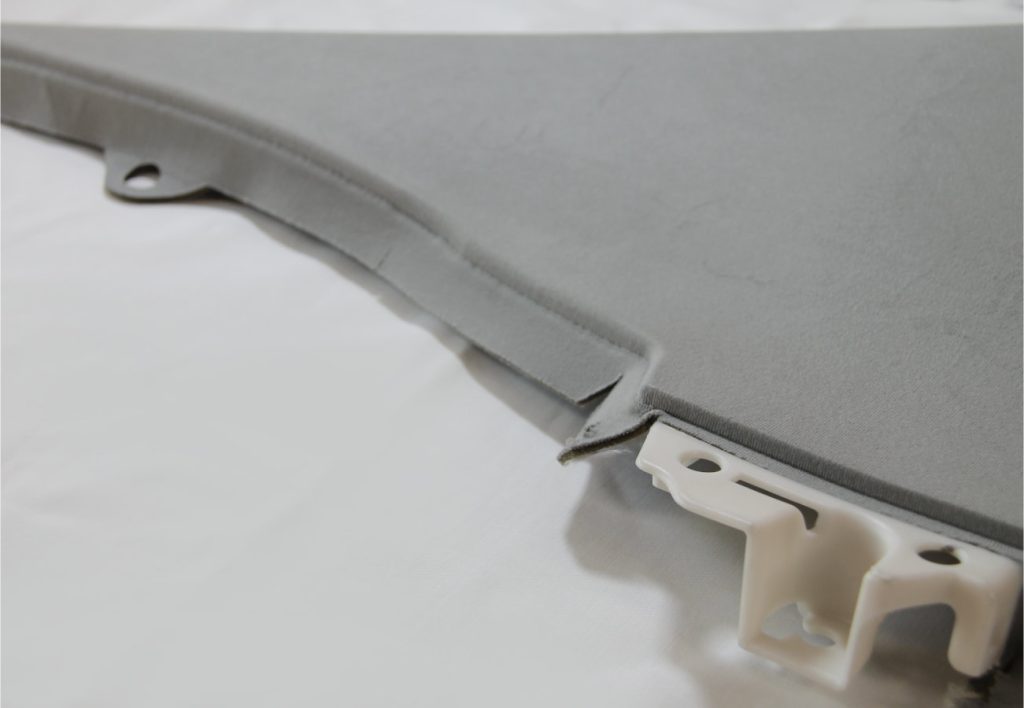
Surface skin inserts
By inserting the skin on the design side and molding it as a one-piece, troublesome post-processes can be eliminated and quality variations can be eliminated.
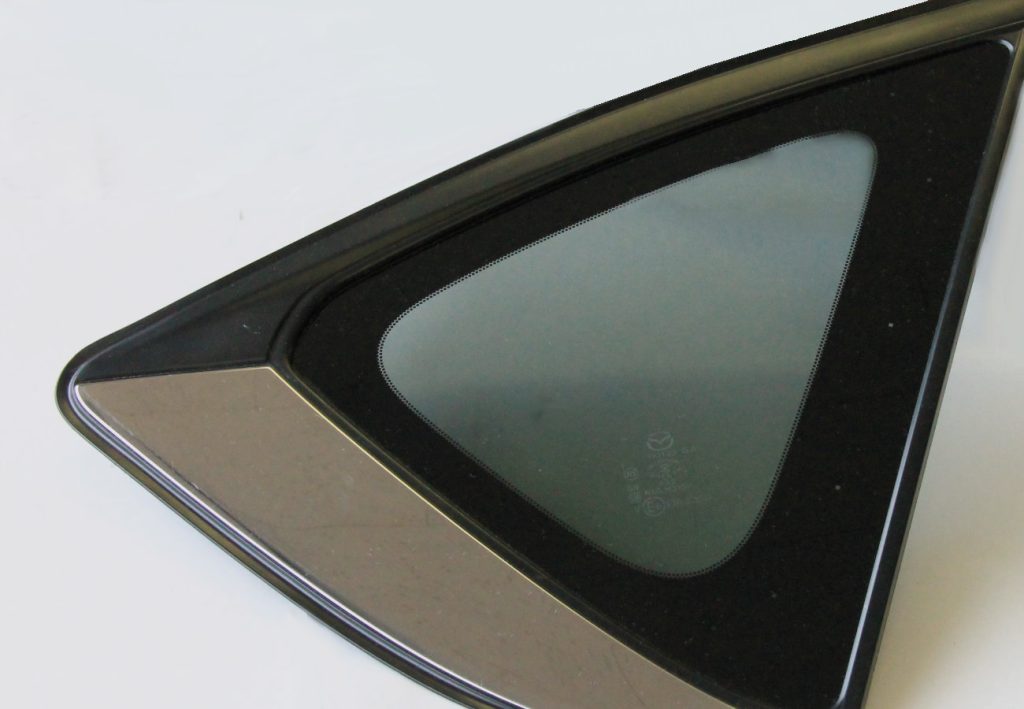
Glass Encapsulation Molding
It is possible to produce 2-sided moldings (no difference in level between glass and resin), which is not possible with the method of attaching weatherstrips after molding.
Resin clips, SUS moldings, and steel plates for reinforcement can be molded together.
English page navigation

Molded products
“KATACHI” makes a change
The “products” created from “molds” become a part of our lives.
Ideally, the encounter with that “KATACHI” will bring about a positive change in people’s hearts and minds.
TAKAHASHI SEIKI also takes advantage of the knowledge we have gained over the years to mass-produce products that require advanced molding technology.
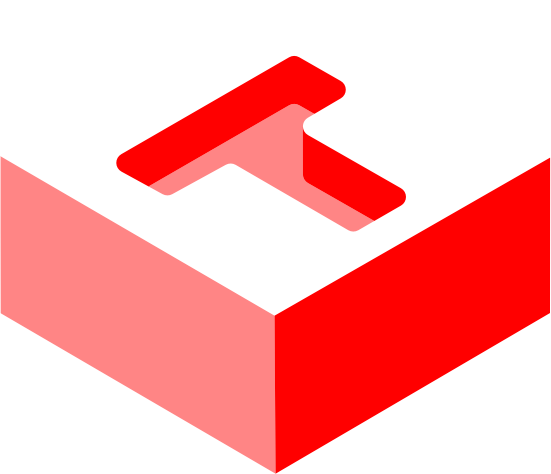
MASS PRODUCED PRODUCT
Mass produced product by TAKAHASHI SEIKI’s production facilities
TAKAHASHI SEIKI also performs mass production of plastic injection molding.
Due to the characteristics of our molding machines, we only have results in special molding applications such as two-color molding and insert molding.

English page navigation
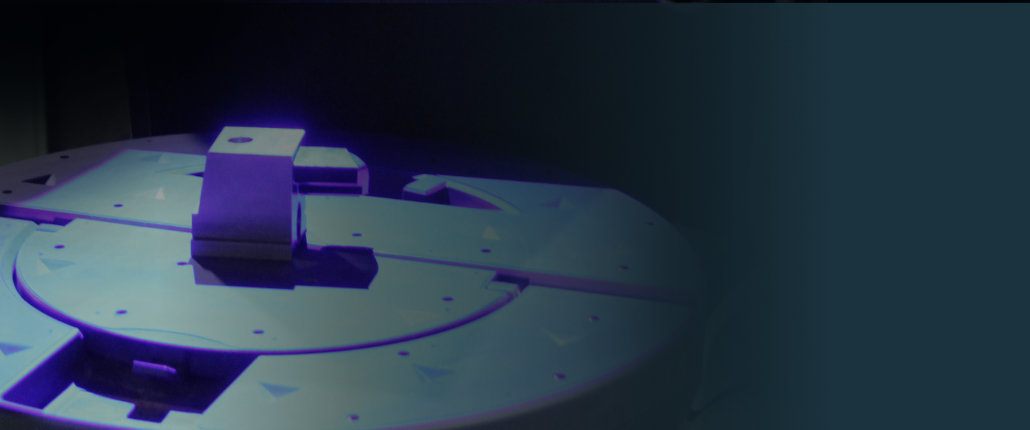
3D Digitizing Technology
From “KATACHI” to next image
From “KATACHI”, we create a world of further images.
It is the beginning of a creation full of new possibilities.
TAKAHASHI SEIKI can convert existing molds and molded parts into data and produce resources for creation.
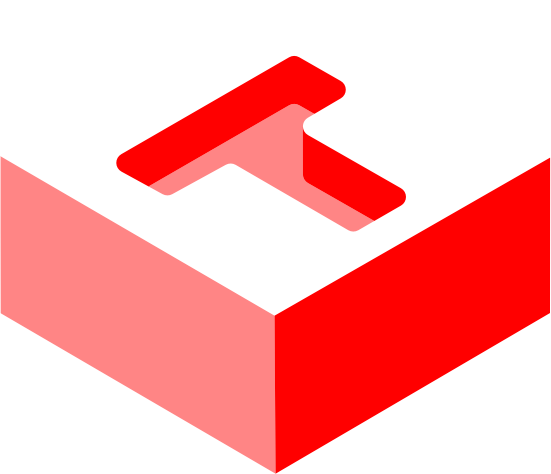
REVERSE ENGINEERING
Reverse engineering with precision measurement technology
TAKAHASHI SEIKI was one of the first in the industry to promote 3D design and the elimination of 2D drawings.
One of the problems is old product drawings with no data.
In the past, we have measured products manually to create product data and re-produce molds, though now that measurement technology has advanced, 3D laser scanning can be used to create highly accurate shape data, which has dramatically shortened the lead time for reverse engineering.
Large molds can be scanned.
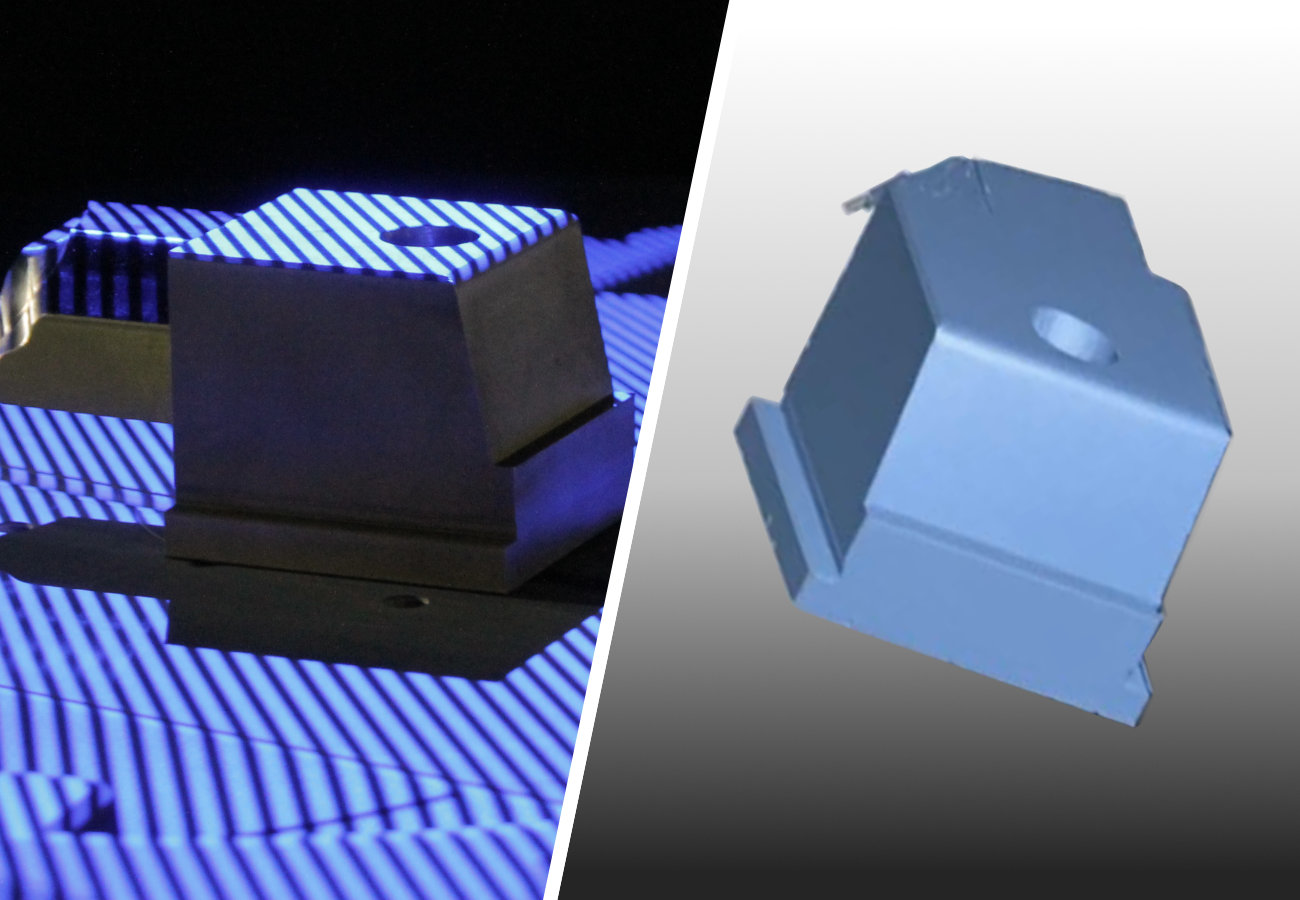
What is reverse engineering?
Reverse engineering” is a composite of the words “reverse” and “engineering (design and manufacture).
In contrast to the general manufacturing process of designing and manufacturing a product, reverse engineering refers to the process of going backwards from an existing product to infer drawings, construction methods, principles, etc.
In the case of mold manufacturing, it refers to the creation of drawings (data) and products from existing molded products and molds.
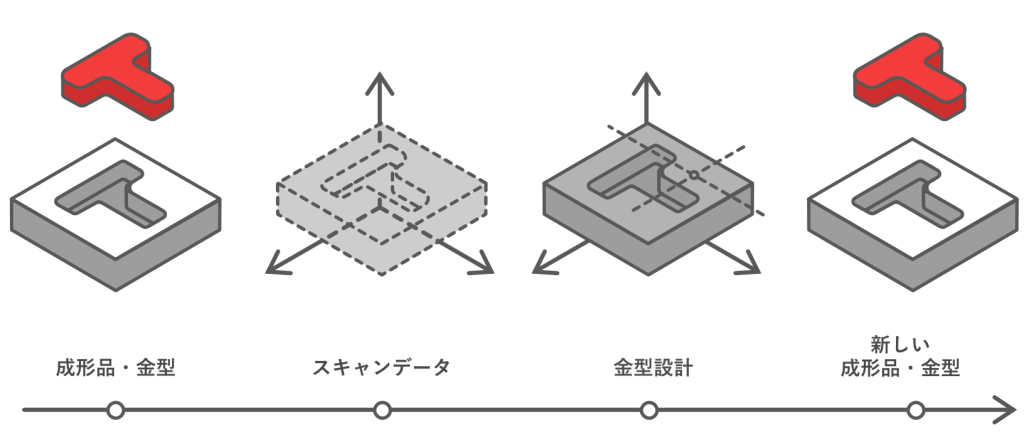
TAKAHASHI SEIKI’s reverse engineering can, for example, answer the following needs
- To convert existing old molds and molded products into 3D CAD data
- Reproduce mass production molds from the product
- Re-manufacturing only the design side of a mold that has deteriorated over time
- Data conversion of manually modified mold geometry
- Grasp how much the dimensions of the molded product differ from the design data. etc…
English page navigation

Molding Machine
Mechanisms for producing “KATACHI”
All it takes to turn IMAGE into “KATACHI” is a system that faithfully reproduces the ideal and an optimized mold.
TAKAHASHI SEIKI’s advanced mold technology is based on our experience in developing molding machines as a world leader.
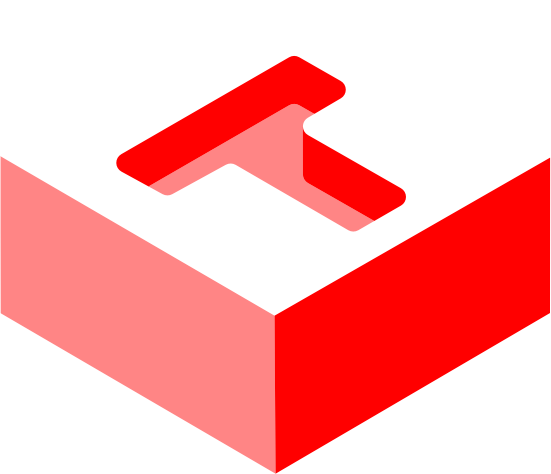
MOLDING SYSTEM
Pioneer of plastic molding system
The development of TAKAHASHI SEIKI’s molding machines has been one of our core businesses since the beginning of TAKAHASHI SEIKI.
We have been building systems together with our customers to meet the demands of the times and to pursue productivity and ease of use.
All of the machines are mainly hydraulic and pneumatic, and we are not taking orders due to the current trend that requires all electric power.
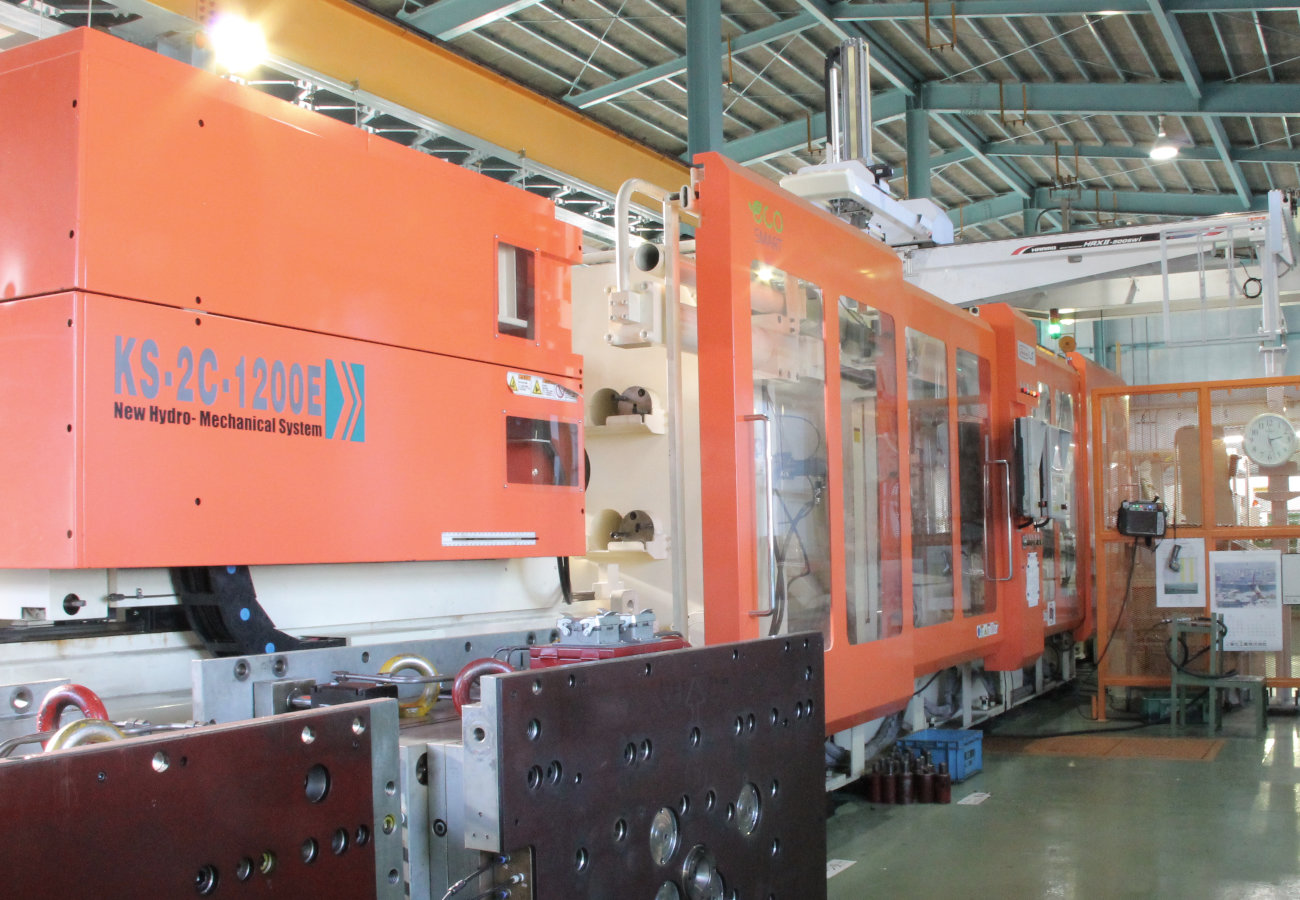
TAKAHASHI SEIKI’s Molding System
- Multi-Color, Multi-Material Molding System
- Insert/Glass Encapsulation Molding System
- NC Blow Molding System
- NC Hot Flow Stamp Molding System
MULTICOLOR MULTMATERIAL MOLDING
Multi-Color, Multi-Material Molding System(2 Color Molding System)
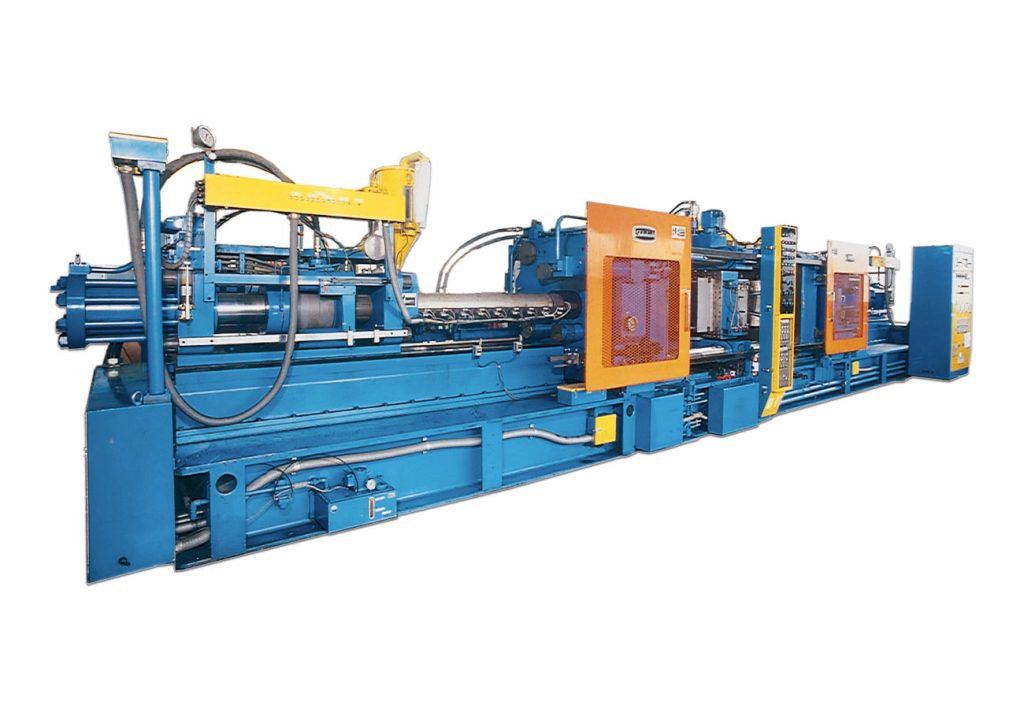
What is a multi-color, multi-material molding system (2 color molding machine)?
2 color molding machine is a technology that injects resins of different colors and materials into a mold to form products that are integrated inside the mold.
2 color molding requires not only a special mold but also a special molding machine.
In 1959, TAKAHASHI SEIKI developed Japan’s first 2 color injection molding machine and established 2 color molding technology.
Since then, TAKAHASHI SEIKI has supported Japanese production technology by providing molding technology that meets the needs of the times through continuous improvements.
We have developed up to 4 color molding machines, and TAKAHASHI SEIKI named the term “Two-Color Molding”.
- Injection units are placed facing each other, enabling molding with half the clamping force compared to other methods.
- No mold thickness limitation as in other methods because the molds on the two sides are clamped independently of each other.
- If the turning plate is stopped at the 90-degree position as a rotary specification, it is easy to add an insert process, etc.
- Since there is an ejector mechanism in the turning plate, general-purpose molding is possible with two sets of normal general-purpose molds by stopping the inversion.
ENCAP MOLDING
Insert/Glass Encapsulation Molding System
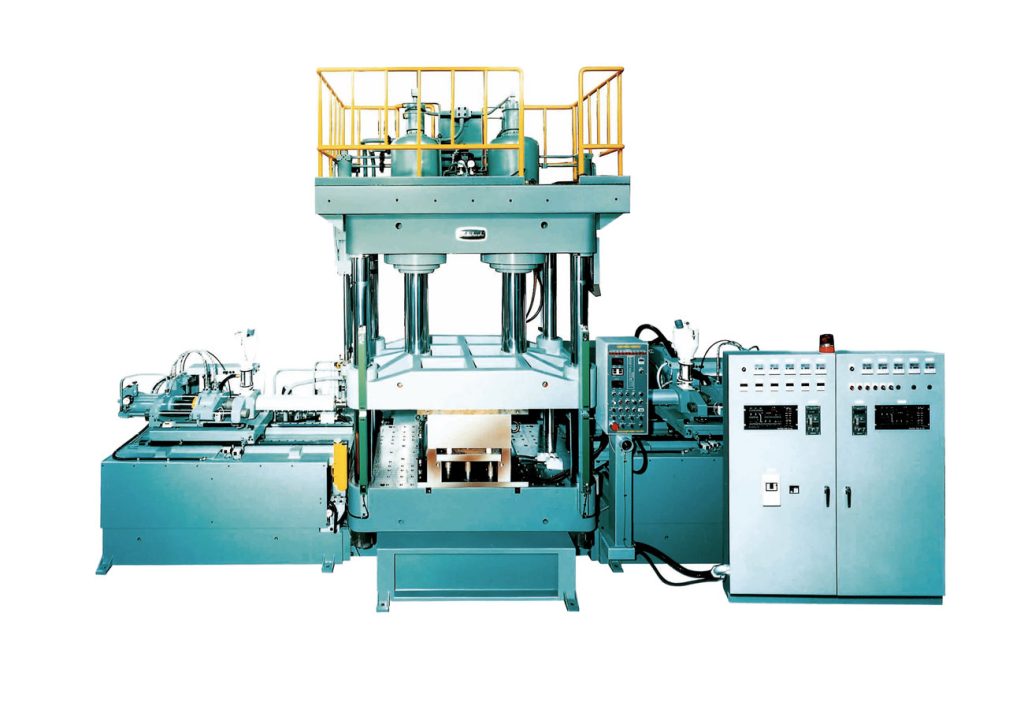
What is Insert/Glass Encapsulation Molding System?
This is a technology in which glass or other materials are inserted into a mold and molded as one piece with plastic.
In order to insert glass that “breaks if dropped” into the mold, a molding machine that could open and close the mold vertically and place the glass in the lower mold was necessary.
As a result of our focus on the evolution of specialized molds, we are now able to mass-produce glass products using general-purpose horizontal molding machines, but we continue to be active as a specialized machine for special molding applications.
- Vertical press machine that can easily insert multiple parts in the die.
- Two injection units are located on both sides of the vertical press machine to handle two sets of products.
- Prioritizing workability, a lower mold is equipped with a movable die plate that can be slid toward the front.
- Expansion to 2 color molding is also possible depending on mold specifications
NC BLOW MOLDING
NC Blow Molding System (Blow Molding Machine)
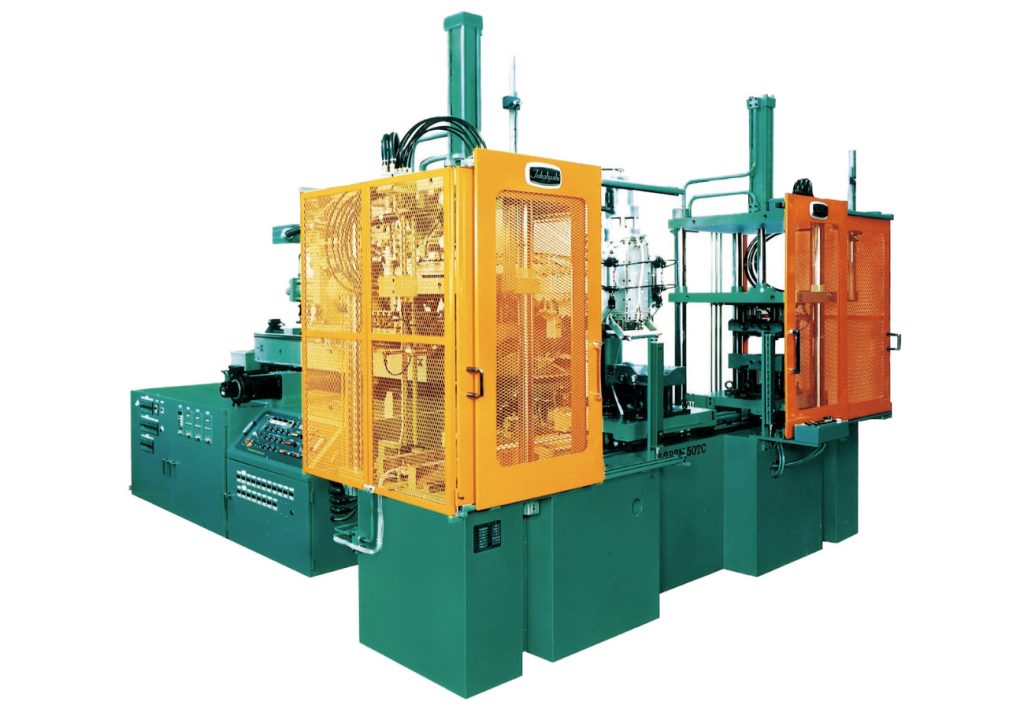
What is NC Blow Molding System (Blow Molding Machine)?
Blow molding is a molding method suitable for producing plastic hollow molded products. Compressed air is blown from the inside of the plastic mold to inflate it and transfer the shape of the mold.
We are good at 2 color molding, so why can’t we do two-color blow molding? This system started with the request, “If we are good at 2 color molding, why can’t we do 2 color blow molding?
The method of placing the mold flat on a vertical press and inserting the parison from the side with a head was very innovative in the blow molding industry.
This system was highly evaluated for its merits beyond the ability to mold ducts made of different materials without assembly, and we have received numerous awards for it.
- NC-controlled head positions the parison along the product shape of the mold, enabling burr-free 3D shape blowing.
- Hard and soft parts are molded as one piece using parison molded from different materials, greatly reducing the assembly process.
- Twin-clamp system shortens molding cycle time and a single machine can mold two types of products at the same time.
- Injection molding with a screw instead of extrusion, which allows kneading of glass fiber and other materials.
HOT FLOW STAMP MOLDING
NC Hot Flow Stamp Molding System (Compression molding machine)
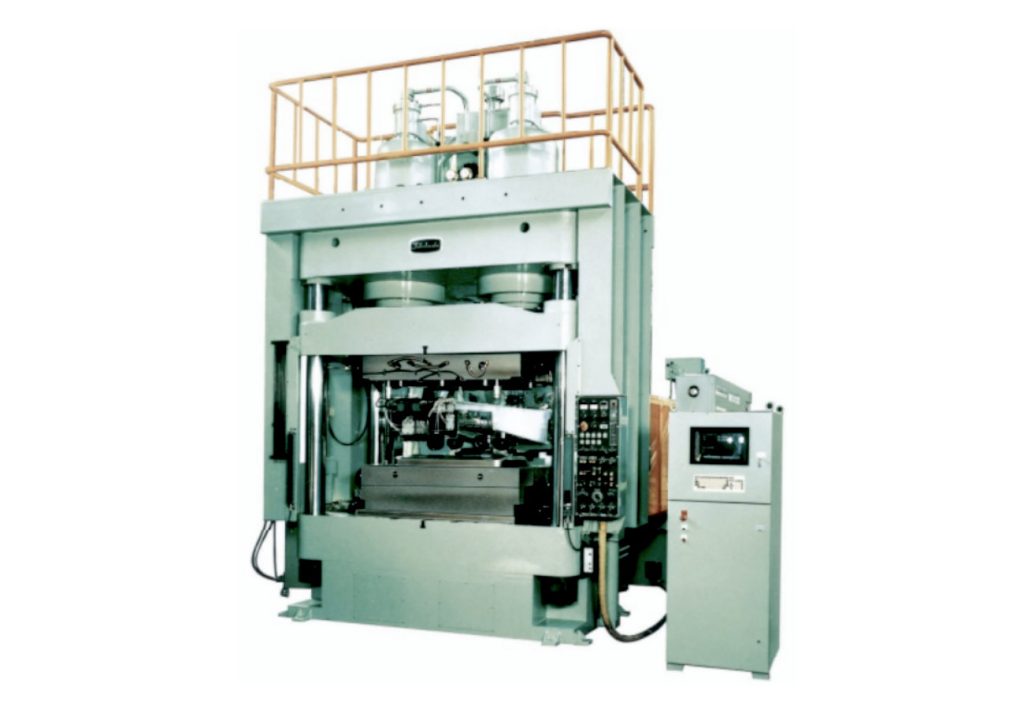
What is NC Hot Flow Stamp Molding System (Compression molding machine)?
In this method, plastic material is extruded into the lower mold, the upper mold is closed, and heating causes the softened resin to flow, resulting in molding.
The so-called compression molding is a molding method that is very compatible with small-lot, high-mix products,
It has been highly evaluated as a molding system that streamlines production, saves energy, and realizes low equipment costs.
- NC-controlled head enables plastic sheet to be aligned along the product shape in the mold.
- Low molding distortion and thin-wall molding are possible.
- No gate is required for the product, resulting in cost reduction due to material loss and reduction of finishing process.
- Wide range of material selection, easy molding of polymer/fiber-containing resins
- Easy one-piece molding by back-shotting plastic sheet onto the inserted skin.
- In-mold reproduction of grained shapes by controlling the shape and position of the insert skin.
English page navigation
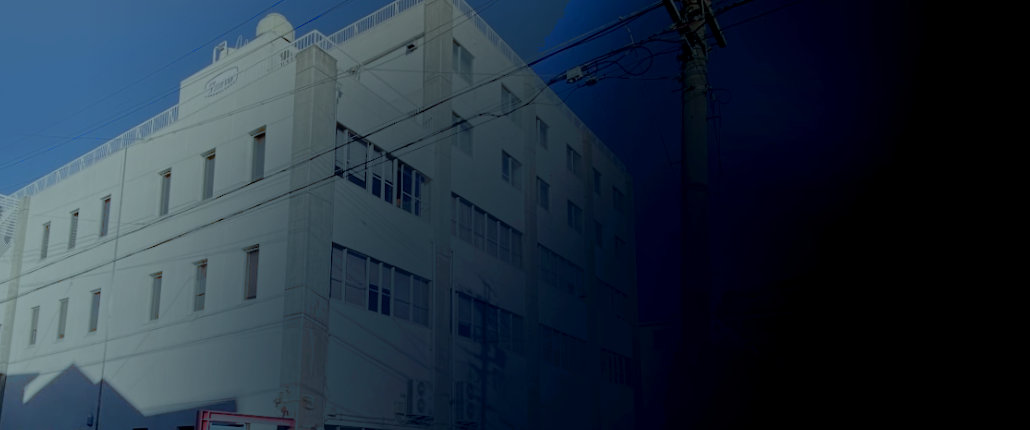
Company Information
MESSAGE
Greetings from the President
For more than 70 years since our founding, we have been striving to manufacture high-quality, high-precision molds,
We have been pursuing answers to difficult problems that cannot be solved with molds by expanding our scope to include molding machines and molding methods.
Fortunately, we have been consulted by many customers, and we have developed new technologies and products that have never existed before.
We have received very high praise for our achievements, and we are proud of the fact that they are still passed on as the challenging spirit of our employees.
We will continue to face each and every mold with the skills and spirit of craftsmanship by combining the latest technology, which continues to evolve day by day, with the “human hands” that are indispensable in mold making.
Takahashi Seiki Co.,Ltd.
President Toshitaka Takahashi
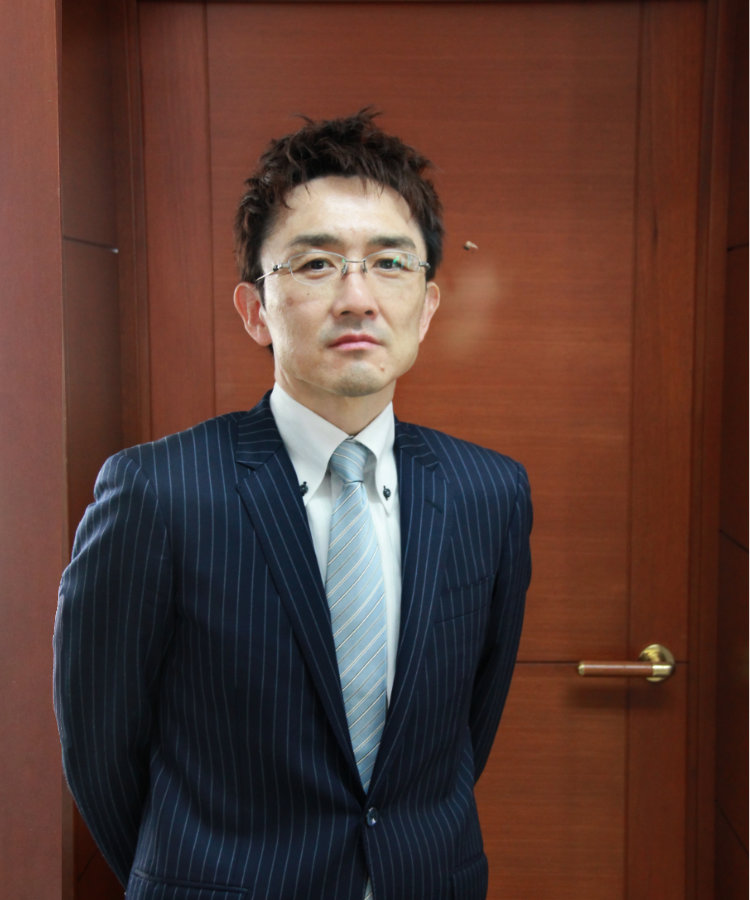
CORPORATE PROFILE
Company Overview
Company Name | Takahashi Seiki Co.,Ltd. |
President | Toshitaka Takahashi |
Location of Head Office Nagoya Factory | 457-0007 1-7-38, Kakegami, Minami-ku, Nagoya-shi, Aichi, Japan TEL:+81-52-811-2126 Email:nagoya@takasei.co.jp |
Location of Anjo Factory | 446-0011 1-2 Kitaura, Kitayamazaki, Anjo, Aichi, Japan +81-566-76-5178 |
Certification | The Japan Die & Mold Industry Association(JaDMA) Nagoya SDGs Green Partners ISO 9001:2015 ISO 14001:2015 |
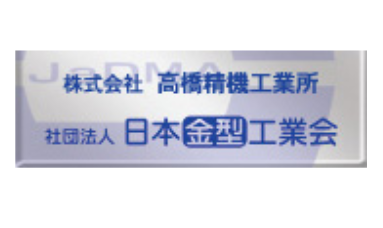
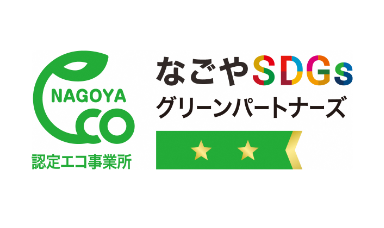
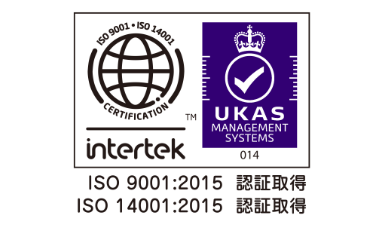
Quality Policies
Faster with better products
- We will focus on customer requirements and strive to improve customer satisfaction.
- We comply with laws, regulations, and rules, and provide products that meet the requirements.
- We will implement improvement activities aimed at manufacturing high quality products.
- Continuously improve the effectiveness of our quality management system.
- We will make our quality policy known to all employees and those who work for our company to raise their awareness of quality.
Environmental Policies
We clearly understand the environmental impact of our activities related to the manufacture of molds, machines, and molding products and services.
We clearly understand the environmental impact of our products and services, and at the same time, clarify the laws, regulations, agreements, and industry requirements related to these activities.
We will also clarify laws, regulations, agreements, and industry requirements related to these activities and set environmental goals for the entire company and each department,
We will continuously improve our activities to prevent pollution and improve the environment.
- We will comply with laws, regulations, etc., and set and manage our own standards as necessary.
- We will promote waste reduction, resource conservation, reduction of defective products, and energy conservation.
- We will strive for environmental harmony with the local community and actively participate in local environmental protection and maintenance activities.
- We will establish our environmental policy in writing, make it known to all employees and contract workers, and encourage them to implement it.
OUTLINE
History
1945 | Founder Kiyoshi Takahashi established “Takahashi Seiki Works”. |
1952 | Reorganized as Takahashi Seiki Co.,Ltd. with capital of 500,000 yen. |
1959 | The first 2 color injection molding machine made in Japan is completed. (injection molding machines are mutually adjacent) |
1962 | Anjo Factory was built. |
1968 | A patent was obtained for the prototype multicolor injection molding process. |
1972 | Nagoya head office building was completed. |
1975 | Patents were obtained in the U.S. and West Germany for a multi-color (multi-material) injection molding machine. |
1980 | The 10th Automated Machinery Development Award by Japan Society for the Promotion Machine Industry received. (3D NC Blow Molding Machine) |
1984 | The joint venture “T.D.Mold Center Co.,Ltd.” was established “Dalian Plastic Co.,Ltd.” in China. |
1988 | Shigetoshi Takahashi succeeded to president. |
1990 | The joint venture “BANGKOK TOOL & MOLD Co.,Ltd” was established with “BDI Co.,Ltd.” in Thailand. |
1995 | 50th Anniversary |
2009 | Technology Award by Toyota Boshoku Corporation received. |
2016 | Presented actual examples of resin molding development.in The Japan Fluid Power System Society. |
2023 | Toshitaka Takahashi succeeded to president. |
ADDRESS
Address
Nagoya Factory
457-0007 1-7-38, Kakegami, Minami-ku, Nagoya-shi, Aichi, Japan
TEL:+81-52-811-2126
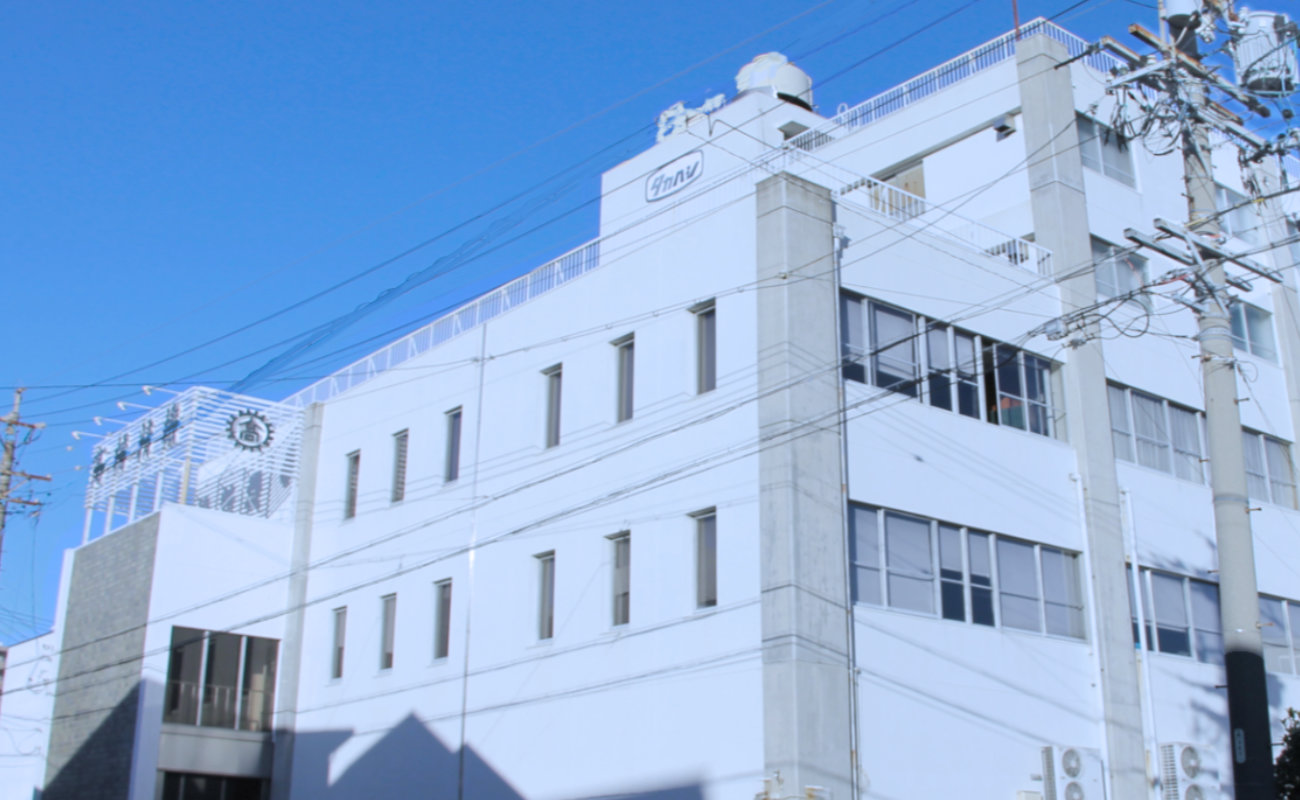
Anjo Factory
446-0011 1-2 Kitaura, Kitayamazaki, Anjo, Aichi, Japan
+81-566-76-5178
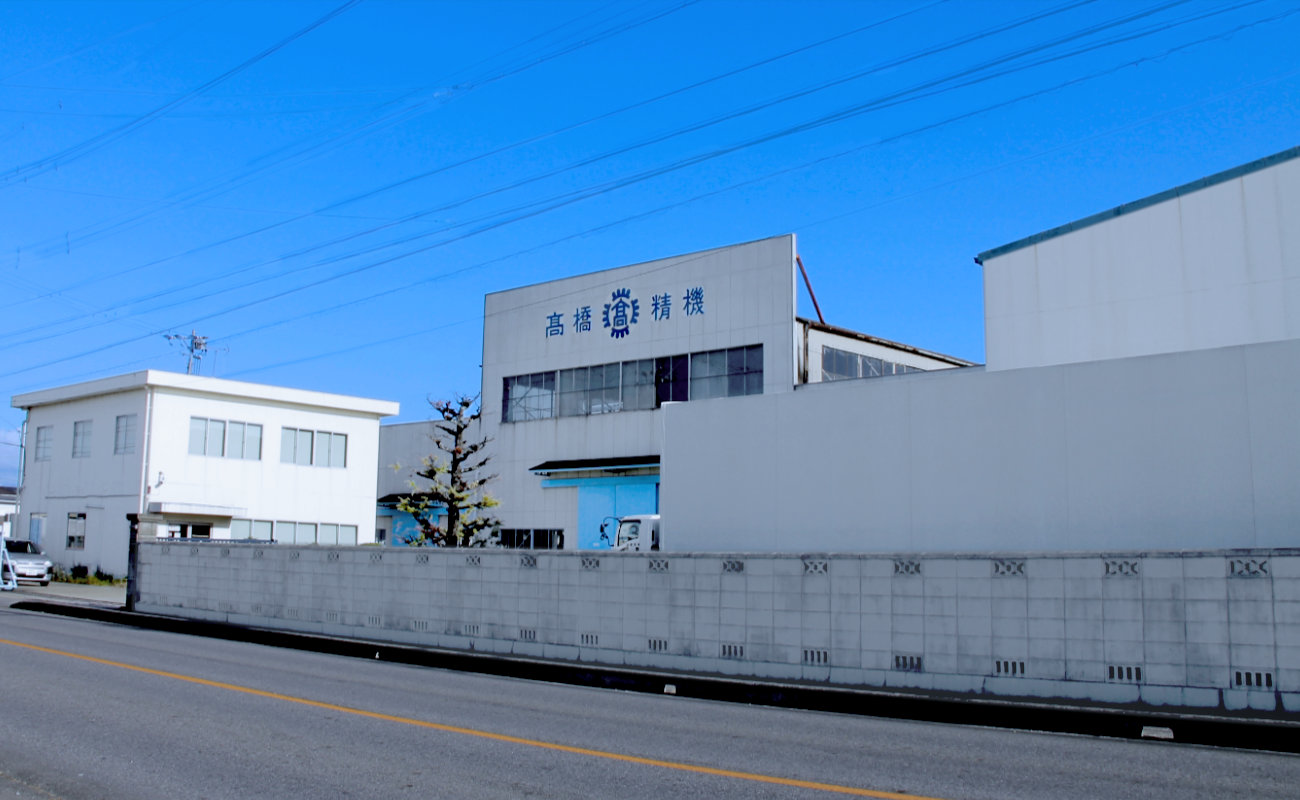
English page navigation
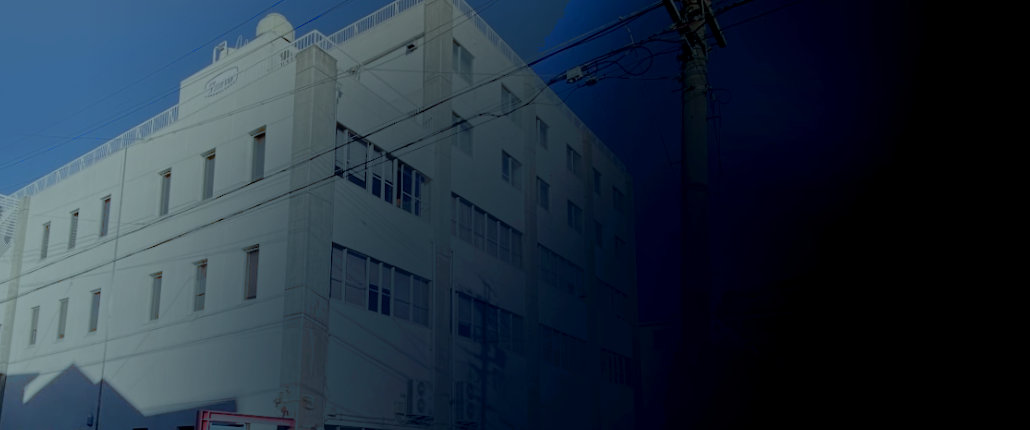
Contact us
Contact us by e-mail
nagoya@takasei.co.jp